Establishing a solid workplace safety model is crucial for the success of any company. There are many different types of safety programs in the workplace. This article will explore Behavior-Based Safety (BBS) programs, an effective safety tool used to identify and reduce workplace injuries.
What is Behavior-Based Safety?
The Behavior-Based Safety (BBS) model uses safety observations, which are effective in fostering safer work environments. Behavioral safety is the systematic application of psychological research on human behavior to workplace safety problems. Studies have revealed that 96% percent of all workplace accidents are triggered by unsafe behavior, which indicates that most accidents are highly preventable.
Here’s some information about these techniques and safety observation examples to better understand a Behavior Based Safety BBS workplace model.
A Good Behavior-Based Safety Program Will:
- Reduce Accidents, Near Misses, and Property Damage
- Improve Quality
- Reduce Absenteeism
- Maintain a Healthier Work Force
- Decrease Injury & Illness Rates
- Improve Workers’ Feelings About Their Work
- Elevate Safety to a Higher Level of Awareness
Behavior-Based Safety Observations Quickly Defined
In the context of a behavior-based workplace safety model, safety observations are performed by competent onlookers who count how many safe and unsafe conditions or actions are identified in a specific work area for a set period of time.
Safety observations can be tallied daily, weekly, or at any other interval desired and are usually recorded via checklists by safety managers, in accordance with company policies. These checklists often have different sections for specific safety topics.
A Few Examples of Safety Observations
Safety observations are easily noted on a checklist of workplace safety goals. For example, a competent onlooker may use a personal protective equipment (PPE) checklist to record whether workers have proper PPE for the job, whether they’re wearing that PPE correctly, and whether the PPE they do have is in good enough condition.
As a further example, a competent onlooker may use a housekeeping checklist to indicate whether workers are using areas for their proper purpose, keeping areas clear of any obstructions, storing any work materials stored safely, and disposing of hazardous materials properly.
Safety observations also help to identify if workers are routinely following established procedures when using tools, ladders, and machinery. A single checklist may include multiple safety topics.
The Key to Successful Safety Observations
Safety observations are a powerful way to identify unsafe conditions so that corrective measures are taken. It’s equally important to record and celebrate positive workplace safety behaviors. Acknowledging good safety behavior on the part of workers who consistently do the right thing strengthens workplace safety culture and morale. Positive reinforcement increases the likelihood that safe workplace behavior will continue.
This is, of course, the goal of a behavior-based workplace safety model – to make the workplace as injury-free as possible by reinforcing safe behaviors and discouraging unsafe ones, all while keeping workers engaged in the process.
Beacon's Safety Services
Beacon Mutual is proud to provide loss prevention and ergonomic services at no additional cost to policyholders. With a large team of safety experts from various disciplines, Beacon's Loss Prevention Representatives and Ergonomic Specialists will outline the steps needed to establish an effective loss prevention program. Our goal is to help establish a realistic safety process to prevent injuries and accidents, improve employees’ attitudes toward safety, and minimize claim costs.
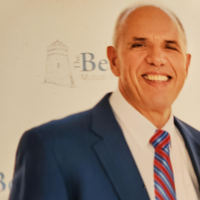
Written by
Guy Lanzi Beacon Loss Prevention Consultant